For the weather in the house
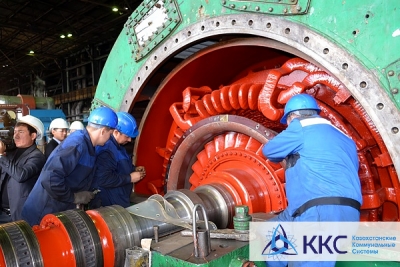
Wednesday, 28 June's 2017
“They plan to repair the boiler by August 6, the cost of the work is 1 billion 272 million tenge,” says Rustam Abulgafarov, chief engineer of the thermal power plant. – A complete replacement of screen pipes and a 10-ton screen steam heater is underway. We will completely renew all 390 pipes of the strip steam heater, replace the second-stage water economizer, and the HPC piping, which is 2.99 tons. Plus auxiliary equipment - smoke exhausters, rotating mechanisms, hot blast fans, augers, and so on.
The numbers sound impressive. To make it more impressive, we note: the screen pipes on the boiler are 146 tons, and if you add them with the pipes of the air heaters, then this together will amount to as many kilometers as the distance from Karaganda to Astana - approximately 200 kilometers. The expected effect of a major overhaul is the replacement of boiler components that have exhausted their service life and an increase in reliability. The boiler will also increase productivity - it will produce not 380-390, but 420 tons of steam per hour. This means that this heat factory will become even more productive. Also at CHPP-3, current repairs of boiler unit No. 8 are underway, the work here is 60% completed. There are also two turbine units undergoing ongoing repairs. On July 1, a major overhaul of turbine No. 1 will begin. It will last until the start of the heating season. Even more impressive is a walk inside the thermal power plant and across its vast territory. Last year, a new power unit was launched at Karaganda CHPP-3, which made it possible to increase capacity to 670 MW. The installation and commissioning of modern, cutting-edge foreign-made equipment was carried out by foreign specialists.
With the launch of the new power unit, the second stage of the expansion project of the Karaganda CHPP-3 (2012–2016) was implemented. Its cost is 185 million US dollars. Thanks to the successfully implemented project, 55 new jobs were created at the thermal power plant.
The first stage started in 2009. Then they invested 86 billion tenge. The funds were used for major repairs of boilers and turbines and the construction of turbine No. 5, cooling tower No. 4 with a capacity of 25 thousand cubic meters per hour and the construction of a new unit with a capacity of 670 Megawatts.
“The management company “Kazakhstan Utility Systems” puts a lot of effort, energy and investment into our CHPP-3, allocates money, does everything for the development of the enterprise,” Rustam Abdulgafarov tells reporters.
The visible effect of the expansion of CHPP-3 is proudly shown to media representatives. We are at the turbine control point. Its technological process is controlled from a single panel. All main indicators are displayed on monitors.
And these small plastic boxes compared to the size of boilers and turbines would hardly attract our attention. Meanwhile, these are objects of new technology, which is being used in Kazakhstan for the first time. It is used at turbine unit No. 4, where ongoing repairs are being carried out until the end of June.
– As a result of the fact that the exhaust steam is cooled on the condenser tubes, deposits occur there and the cross-section of the tube narrows. We carry out biological treatment of condenser tubes,” explains the chief engineer.
Simply put, it's like limescale in a kettle. There are many ways to get rid of it on a turbine scale - hydrodynamic, magnetic, ultrasonic. You can wash the tubes with hydrochloric acid. But its import and disposal is a very troublesome and expensive matter, and it is easy to damage the unit. Therefore, Karaganda Energy Center decided to turn to advanced technologies. Cleaning of turbine condensers is carried out according to plan. If it shows its effectiveness, biotechnologies will be given the green light.
And we are talking specifically about biotechnology. Special microorganisms produce weak acids during their life processes and simply feed on harmful deposits. And then washed off with water. Bacteria are selected individually for specific equipment. A sample of the station’s fourth turbine was sent to the laboratory of the supplier company, where chemists selected the composition of the strain and determined the operating regulations of the bacteria. Cleaning can take from a day to a week. The shelf life of bacteria in closed containers is six months. After cleaning, fuel consumption will be reduced, vacuum and water circulation will increase and exhaust temperature will decrease. In a word, the scale will disappear from this huge “kettle”, and it will begin to work more efficiently. This is what the consumer requires from the equipment and the service provider as a whole.